Introduction
Regional Cluster Name: Estonia
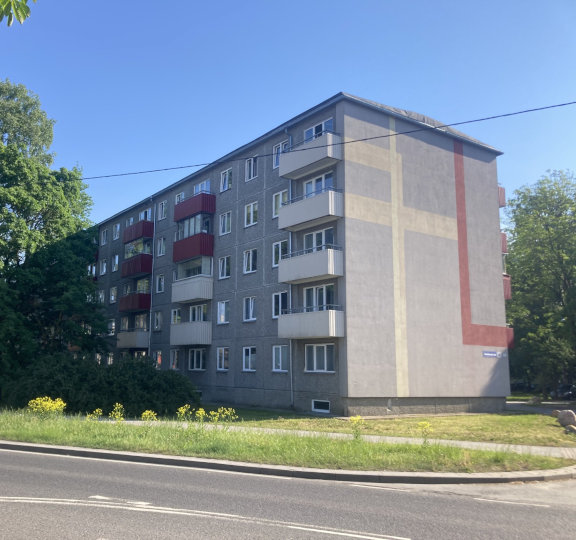
The Estonian pilot building is a typical mass-construction apartment building, constructed by using prefabricated concrete large panels. This type of prefabricated panel buildings were spread all over the Soviet Union in the 1950s and the 1960s (until 1990), where most of the housing was destroyed during World War II.
Today, many Estonian apartment buildings need renovations, due to their low energy performance and construction quality, as the building stock has only been partially renovated in the early 1990s. To minimise disturbances, improve material spending, and reduce waste and time required for renovations, the pilot building is being renovated by using prefabricated timber frame insulation elements.
Location of the building
Estonia
Construction year
1960s
Building use
residential
Energy performance certificate
D
Net floor area
approx. 4000m2
Number of floors
5
Structures
Concrete walls, end-walls insulated with ETICS (EPS)
Heat source
efficient district heating
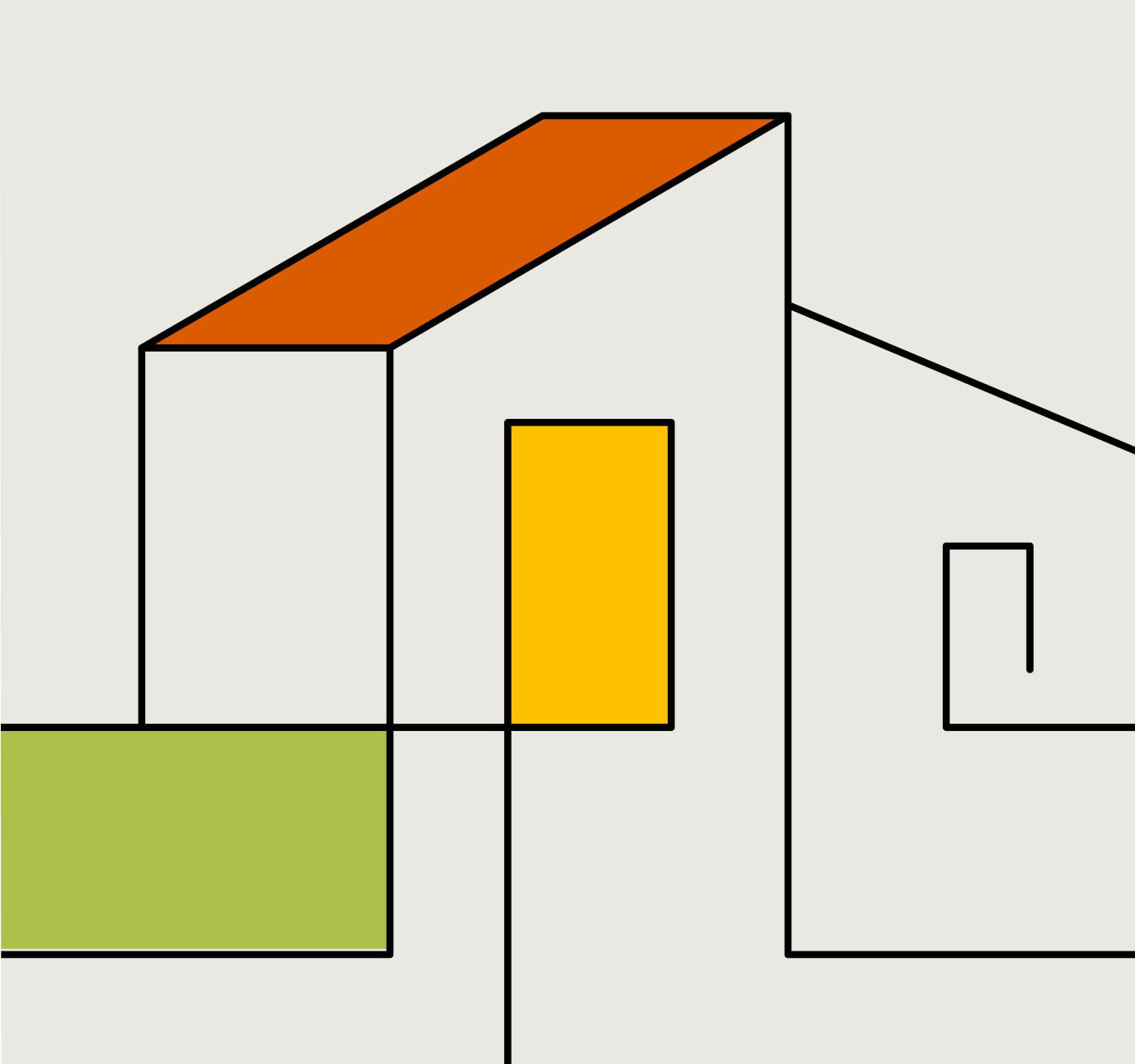
Expected outcomes
- A deep energy renovation with prefabricated insulation façade and roof elements.
- Improvement of energy performance from EPC “D” to EPC “A”
- Reuse of existing materials and components:
- additional insulation of facades without removing the existing ones (decayed and insufficient thickness)
- reuse of windows (in another building or in the renovated building)
- fixing solutions for later deconstruction and reuse possibility,
- reuse of the old concrete
- Prefabricated components: prefabricated bio-based additional insulation (thermal transmittance reduction ~ by a factor of 10) elements for the facade with maximum locally re-used and recycled (circularity index ≥ 0.60) materials and locally based bio-based (timber frame) materials. This construction method results in a short construction (~2 times shorter insulation period) period on sites and occupants will be less disturbed. It is more weather-independent as well.
- Design innovation: design for demounting, later reuse, scan to computer-aided manufacturing (CAM)
- The indoor climate of the building will be improved (from indoor climate category IV to II) by balanced ventilation with heat recovery and room based controlled heating system. Onsite renewable energy will be used and stored for building.
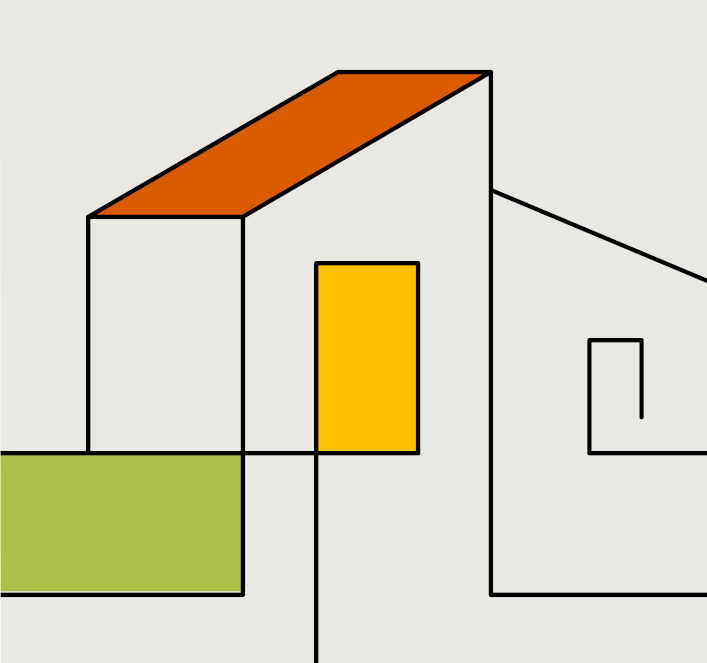
Value chain approach
The pilot aims to adopt an integrated value chain approach, involving stakeholders and building occupants in planning, design, budgeting, procurement, construction, and commissioning innovative renovation solutions. Relational contracting will align objectives and interests, while end users and local authorities will be involved. Sustainability experts will evaluate solutions’ feasibility, and innovative design alternatives will be developed using lean methods and BIM.
Partners
- Coordinator:
- Manufacturer and installation:
- Housing association:
The Estonian Union of Co-operative Housing Associations, EKYL
- Public entity:
Contact information
Targo Kalamees